FRIALEN system: Electrofusion fittings in PE 100 for water and gas distribution pipes
The line includes electrofusion fittings in PE100 and HDPE specific for pressure pipelines, under the FRIALEN brand, long spigot PE fittings for butt welding.
Quality and certification
FRIALEN electrofusion fittings are designed, built and tested according to the highest quality standards and with the most modern technologies. The development of a new product, as well as modifications and updates of existing products are thoroughly checked and tested.
Our continuous Quality Controls extend to FRIALEN electrofusion fittings, to our FRIAMAT welding machines and to the quality of the welding as a result of the optimal union of both components. The reliability and durability of the casting process over time is guaranteed only by using FRIALEN fittings and FRIAMAT welding machines.
FRIALEN electrofusion fittings are subjected to continuous Quality Controls with strict test requirements, which are part of the Quality Control System, Certified according to ISO 9001.
FRIALEN fittings are certified according to DVGW GW335-B2 and are regularly audited by third party bodies. In Italy, FRIALEN electrofusion fittings are certified by the Italian Institute of Plastics which, based on the results obtained, has authorized Aliaxis Germany to affix the mark of conformity to the requirements of the UNI standards on them. FRIALEN fittings also comply with the requirements of Ministerial Decree 174/04 and therefore can be used on pipelines intended for the transport of water for human consumption.
FRIALEN fittings can be welded with pipes having SDR from 17.6 (Smin = 3 mm) up to SDR 11 according to UNI EN 1555 and UNI EN 12201.
PEBD, PE50, PE63, PE80, PE100, PE100 RC and PE-Xa pipes can be welded, whose flow index MFR 190/5 is between 0.2 and 1.7 g/10'. FRIALEN fittings satisfy the requirements according to DIN 16963, part 5 and part 7, as well as UNI EN 1555-3 and UNI EN 12201-3. Welding is possible at ambient temperatures between - 10°C and + 45°C.
Cooling times
For electroweldable fittings, the cooling times indicated in the bar code, marked by the initials (CT) are to be understood as times until welding is completed. In the case of handling collars (DAA) and blank collars (SA), the cooling times indicated in the barcode are to be understood as minimum times before drilling.
The pressure test can be performed after the cooling time has elapsed after welding the branch.
Pressure resistance
FRIALEN fittings are made in PE100. The maximum pressure resistance of the fitting can be determined based on the intended application.
With the relation MOP = 20xMRS/Cx(SDR-1) the maximum pressure can be determined.
MRS = 10.0 (in case of PE100 pipe)
MRS = 8.0 (in case of PE 80 pipe)
C = safety factor:
1.25 for water
3.25 for gas
SDR= d/e with d outside diameter of the pipe and e thickness of the pipe.
FRIAMAT: Multi-purpose welding machines with variable voltage for welding in complete safety
In accordance with the Italian standard EN UNI 10566, the FRIAMAT line includes a range of multipurpose variable voltage welders with traceability functions and welding parameter printing.
The FRIAMAT PRINT ECO is able to weld fittings up to a diameter of 1200, with an absorbed power of 3500 W. The body of the machine is in high resistance thermoplastic resin with IP54 protection degree and the internal software offers the possibility of memorizing 1000 welding processes. welding. The welding cables are 4 meters long with 4 mm connectors, the barcode can be read using an optical pen or miniscanner, with the possibility of selecting the language of use and entering data manually in an emergency. The operating range goes from -20 °C to +50 °C with automatic correction of the welding times based on the ambient temperature detected. Welding reports can be printed with a USB printer connection. Supply voltage 220V. Weight: 18 Kg. Supplied in an aluminum case to protect against accidental blows and provided with a key lock.
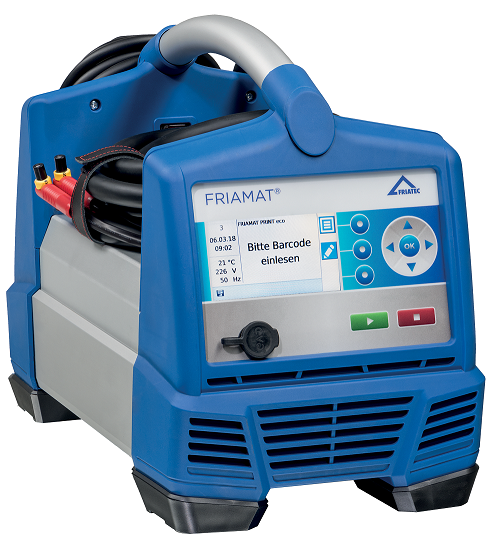
With the FRIAMAT PRIME welding machine, there is the possibility of using the dedicated APP which allows the recording of welding parameter data, the geolocation and the forwarding of all information for operational traceability.
FRIATOOLS: Auxiliary equipment for safe and efficient welding
The range includes numerous tools to be able to carry out welding according to the standard requirements:
- Orbital reamer for PE pipes from d 20 to d 1200
- Aluminum transport cases for reamers
- Manual scraper for pipes and branches from d 32 ÷ 63
- Replacement blades for reamers and scrapers
- Aligners and positioners for sleeves, tees and elbows
- Fixture for DAA and SA saddles
- SA UNI saddle clamping unit
- Drilling device
- Specific cleaner for polyethylene
- Permanent marker for marking the welding area of pipes and fittings